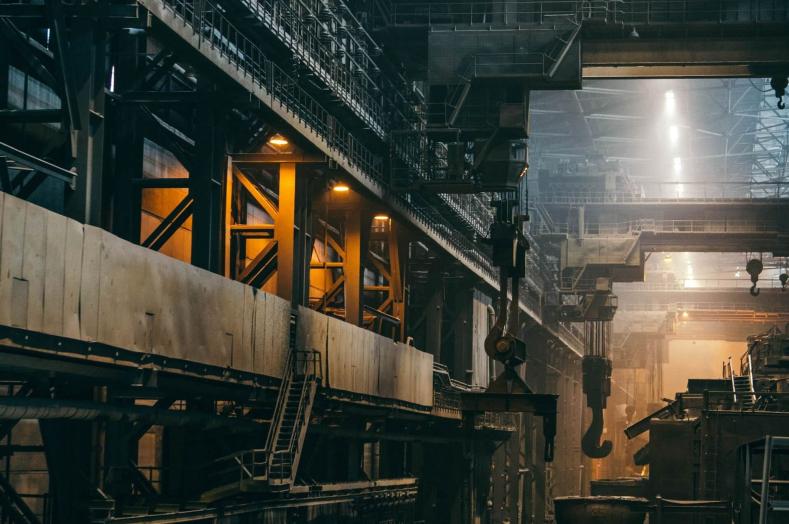
Capacity planning is the process of assessing your current and upcoming projects, and ensuring you have the time, skills, and physical resources to achieve your project goals.
But, how do you plan capacity when supply chain issues make projects grind to a halt? Thanks to a confluence of geopolitical tensions, renewed lockdowns, and increased demand, not everyone can get the materials or components they need.
Yet, this presents an opportunity to change direction. And, the results can be lucrative.
Supply Chain Challenges
Projects that rely heavily on raw materials or outsourced components may stall due to:
- Lack of access to production facilities
- Late delivery of physical resources
Let’s put these into context.
The global semiconductor shortage worsened with the Covid-19 pandemic. This is because many manufacturers stockpiled chips in response to fluctuating demand. Lockdowns, particularly in China, also shrunk chip output considerably, increasing demand even more.
For automakers, this was especially bad news, as there can be up to 3,000 semiconductors in a single car. Ford, Mercedes, and Jeep were among the big names that had to stop or cut back their production.
Supply chain challenges such as these could spell a death knell for some companies. But others learn to roll with the punches. Car companies in particular can replace a component from one supplier with another, for example, to create a simpler dashboard that doesn’t require the same sub-components.
Changing with the Marketplace
Companies have 3 choices when they can’t access materials and complex components:
1. Shift to Another Site
When you can’t access facilities in one country, moving production to another site makes sense. But there are some things to take into consideration.
- Infrastructure access. How close is your new facility to transport hubs? How accessible is your customer base? Choosing the right location can impact your shipping and fulfillment costs, as well as your access to materials.
- Workforce availability. This involves employee capacity planning, as you might need new staff for the new site. However, you could partner with an existing production facility with a workforce already in place. This can result in a tighter turnaround for your product.
Still, switching site usually means increasing lead times. So, if you choose this option, prepare for some downtime and an adjustment to profit projections.
2. Switch Suppliers
Products reliant on materials and components from international suppliers might suffer from longer delivery times or lack of delivery altogether.
You could choose to switch supplier—perhaps to one that’s closer, or in a more politically stable territory. But there are two key points you need to assess before you do.
Firstly, cost. Will the ability to meet demand trump any investment you make with a new partner? Also, you must take into consideration contracts with your current provider. Just because they failed to deliver, doesn’t mean they breached your contract. And consider the cost of not having the necessary component at all. In addition to this, companies may have some wiggle room that allows them to hike up the final price of the item.
Secondly, staff. An onshore supplier might seem like the best solution in the current climate. But do they have any staffing challenges? And, if so, how do they plan to overcome them?
“Supplier diversification and relocation can be costly and impractical for highly complex products. And holding more inventory and building redundant capacity could create inefficiencies in many industries.” - the World Bank
It’s not a decision you can make lightly. You must weigh up whether the current delays in delivery will continue in the long-term, or if there’s an end in sight.
3. Change Design
This is a divisive option. For many companies, it can mean going back to the drawing board.
But it can also provide a more sustainable way to meet future demands.
Again, let’s look to the auto industry and the global chip shortage. Car manufacturers use semiconductors for all manner of things—from airbags to real-time information technology. They could reduce lead time by using easier-to-source products to replace chips where they are less critical.
Capacity Planning to Meet Changing Demands
“Supply-chain shocks” that affect global production occur every 4 years, according to McKinsey. They also cause companies to lose 42% of 1 year’s earnings every 10 years.
Capacity planning that focuses on tried and trusted processes might work most of the time. But, when you face sudden supply chain challenges, flexibility is key. For companies with low profit margins, business agility will be crucial for continuing production and keeping your business above water.
Above all, don’t panic. Change can be profitable. And, when it’s not, it brings lessons that can help your business react better to the marketplace in future.